INTRODUCTION
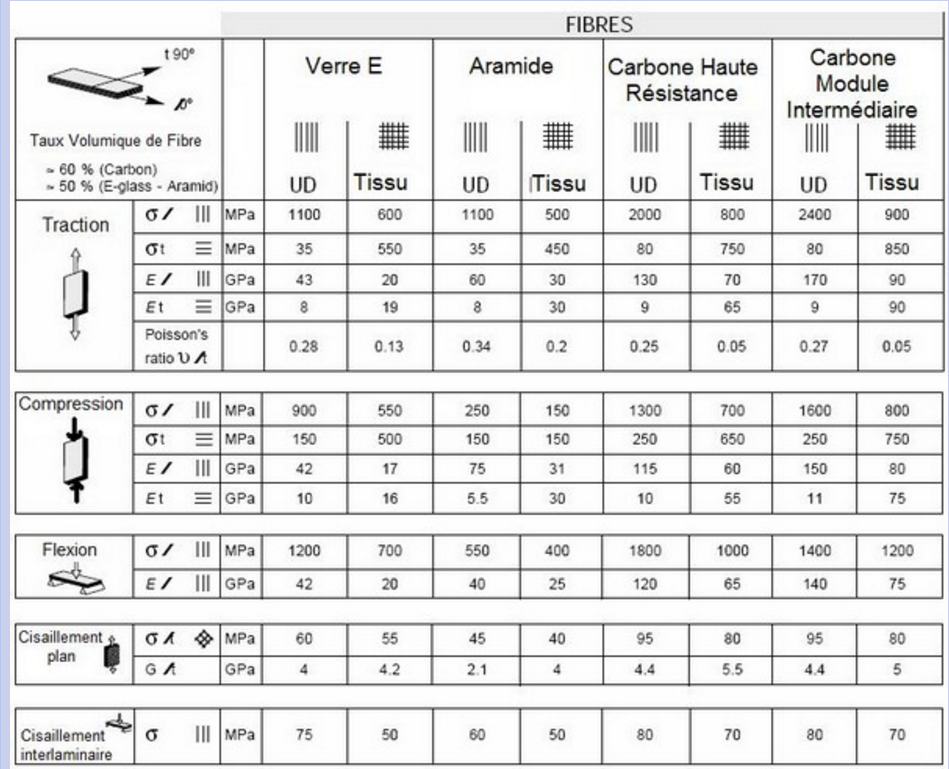
composites epoxy carbone caractéristiques
MATERIAUX COMPOSITES ET ENSEMBLES MECANIQUES
L’introduction de matériaux composites dans les ensembles mécaniques de RARTRIKE-France vient- d’une part de la nécessité, à propriétés mécaniques équivalentes, de rendre l’assemblage plus léger,
- et d’autre part de la possibilité de réaliser ces pièces mécaniques rapidement et à moindre coût sur le site de RARTRIKE-France.
- Il n’est pas adapté d’usiner des matériaux composites en contact avec des pièces mécaniques en rotation. La poussière issue de l’usinage rend en effet très rapidement inopérants les engrenages et roulements qui y sont exposés.
- on ne peut réaliser un engrenage ou un couple conique en composite époxy-carbone, car celui ci est par nature abrasif. Si l’on doit tout de même usiner ponctuellement les composites pour ajuster une dimension ou réaliser un perçage, les surfaces sont stabilisées par une couche de vernis protectrice pour eviter la contamination des éléments roulants par les poussières de carbone.
- Le composite n’est pas un « black métal » : on ne peut transposer directement modules caractéristiques de traction, pression ou cisaillement du métal au compoite epoxy-carbone.
- pour les boîtiers d’assemblages
- comme cage des roulements de centrage,
- comme arbres de transmission de puissance.
- comme supports des pivots de type IGUS* ( pivots de direction et d’inclinaison )
COMPOSANTS MECANIQUES STANDARDS ISOTROPES
Les propriétés des matériaux isotropes sont parfois irremplaçables, c’est le cas de l’acier ou de l’aluminium pour les pignons coniques, les roulements et certains arbres. Le chemin de roulement est le plus souvent constitué par de l’acier, ou de l’aluminium (après écrouissage). Les pignons à chaîne peuvent bénéficier de la légèreté de l’aluminium à condition d’utiliser certains alliages traités thermiquement. Les engrenages standards bénéficient avant utilisation d’un usinage (alésage) pour y placer quand cela est possible les éléments roulants, les arbres composites et diminuer le poids de l’ensemble. Les « nouveaux » plastiques, eux aussi isotropes peuvent, dans certains cas prendre la place de ces derniers avec un atout pondéral évident, une bonne résistance à la saleté et une absence de lubrification. Il s’agit alors de pivot ou de guidage linéaire par exemple. Dans ce cas, le système doit accepter des exigences moins élevées en terme de tolérance mécanique. L’apparition des céramiques dans certains éléments de roulement est intéressante mais son impact est très limité sur la réduction du poids.MISE EN OEUVRE DES MATERIAUX COMPOSITES
la mise en oeuvre des composites epoxy-carbone répond à un certain nombre d’exigences. En dehors de la « cohabitation » avec les éléments roulants des ensembles mécaniques, que nous avons évoqué ci-dessus, le procédé de fabrication des composites structurels doit prendre en compte :- les contraintes mécaniques proposées (épaisseur des structures, composition et orientation des fibres par exemple)
- le procédé d’assemblage des ensembles mécaniques (forme du boitier assemblé)
- les règles de fabrication des composites structurels ( épaisseur constante des éléments de structure par exemple)
- le coût de mise en oeuvre : fabrication des moules, technique (pré-impregnés découpés, injection…)
- la complexité de certaines mise en oeuvre (injection)
- la phase de développement (prototypage, production)
- et bien sûr ce qui est possible de faire : il est impossible d’obtenir par exemple certaines pieces d’un seul tenant par moulage.
- Une partie centrale, qui reproduit la forme des éléments roulants, à tolérance étroite pour les éléments d’appui comme les roulements à bille ou avec un espace laissé libre pour les engrenages,
- un moule externe, facilement démontable ou qui prévoit une dépouille suffisante pour le démoulage.
REALISATION DES ETRIERS DE DIRECTION COMPOSITES
Les étriers de direction étaient constitués originellement (RARTRIKE PJE) d’une pièce de tôlerie pliée en aluminium. Pour réaliser ces étriers de direction en tôle pliée, nous partions de la mise à plat, d’un dessin de découpe et d’un pliage secondaire précis. En réalité, pour le RARTRIKE PJE, les contraintes de positionnement du pivot de direction, de l’étrier de frein et de la fusée nous avaient fait réaliser le pliage avant d’aléser les pièces, ce qui est une procédure très complexe en soi, peu reproductible de surcroit. Nous avons décidé d’évoluer franchement vers des matériaux plus légers et un processus de fabrication simple, reproductible. La forme de cet étrier, qui est l’élément mobile du pivot de direction et le support de centrage de la fusée de roue, dépend de l’angle de chasse et du déport au sol du pivot de direction. La position des points de fixation de l’étrier de frein est très différente à droite et à gauche, car directement liée à la morphologie des freins à dique utilisés (BB7 cables d’AVID, dans le cas du tricycle oscillant alpin.), Les freins à disques que nous utilisons sont destinés à des vélos, où le frein est conçu pour fonctionner d’un seul côté de la roue. Au total donc, les deux étriers de direction ne sont pas simplement « symétriques » mais très différents l’un de l’autre.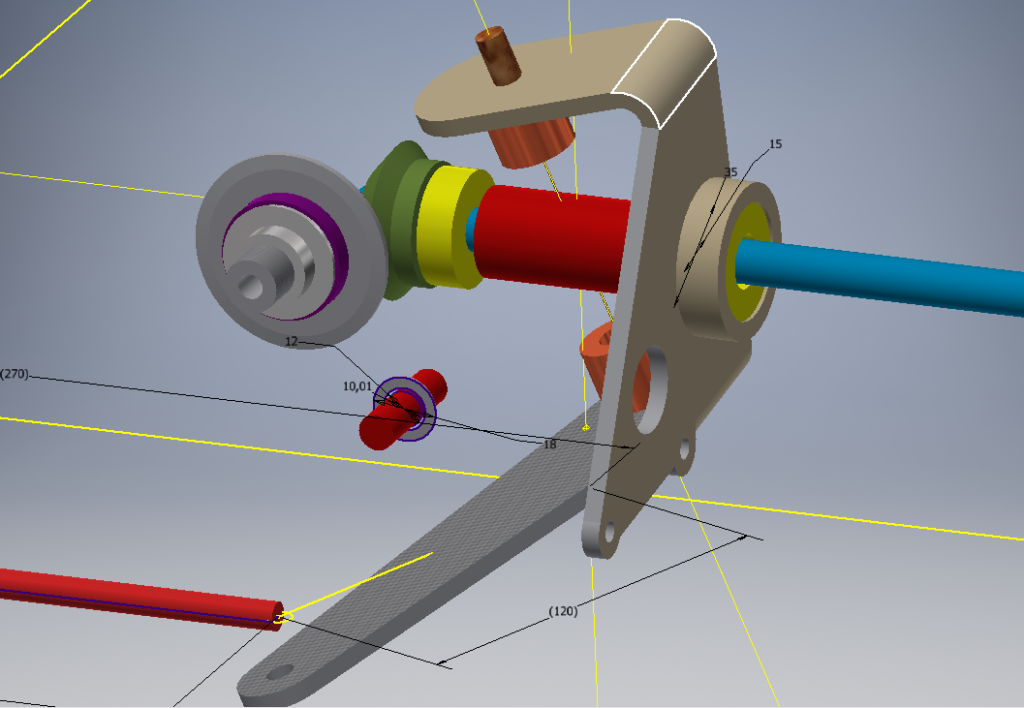
ETRIER DIRECTION GAUCHE VUE POSTERIEURE ET LATERALE
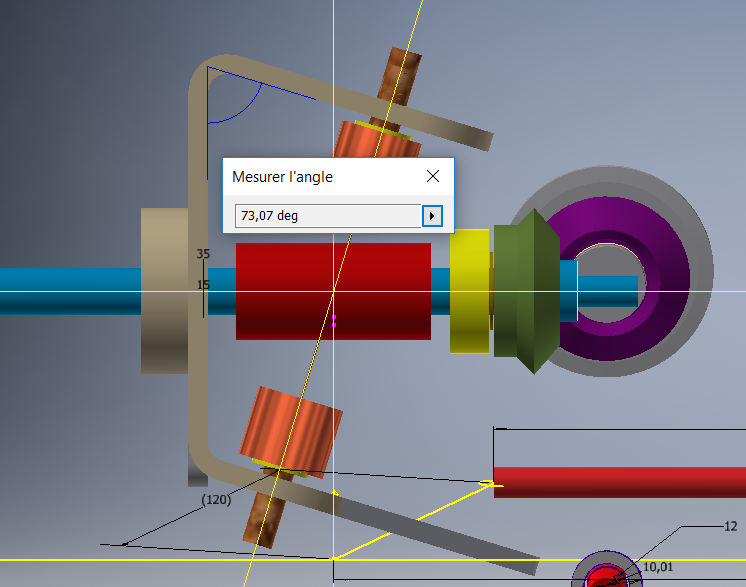
ANGLE SUPERIEUR DE L’ETRIER GAUCHE
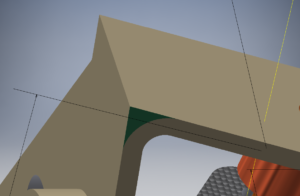
coin de dimensionnement
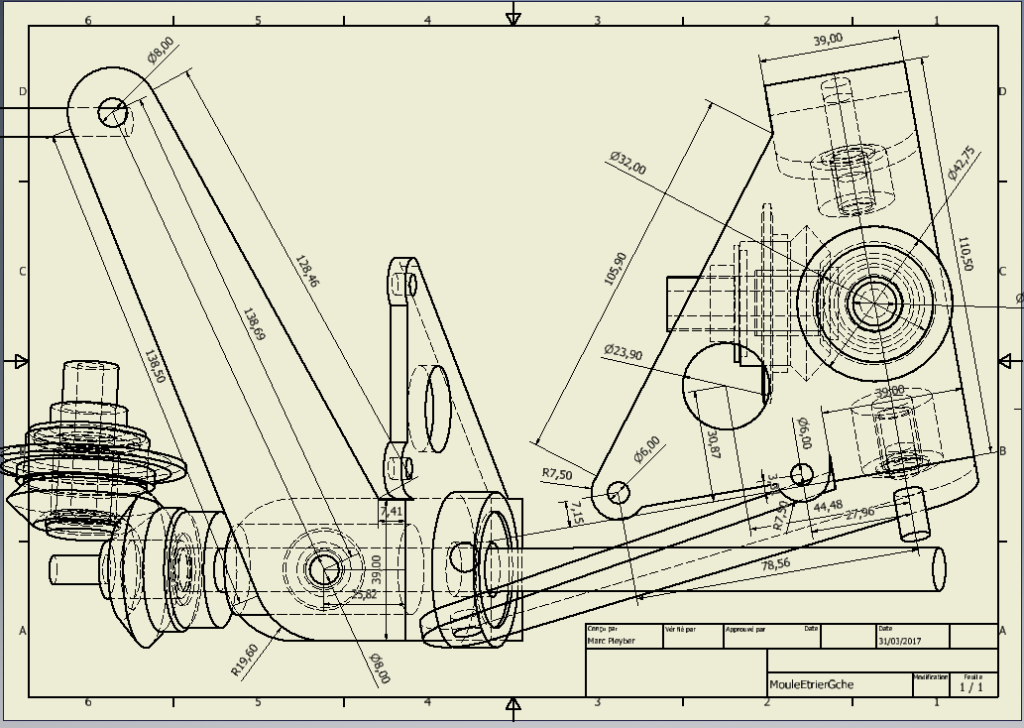
EMPREINTE MOULE ETRIER GAUCHE
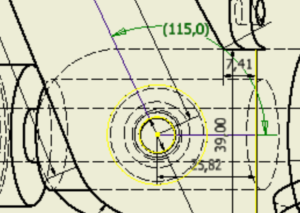
ANGLE BIELETTE DIRECTION ETRIER GAUCHE
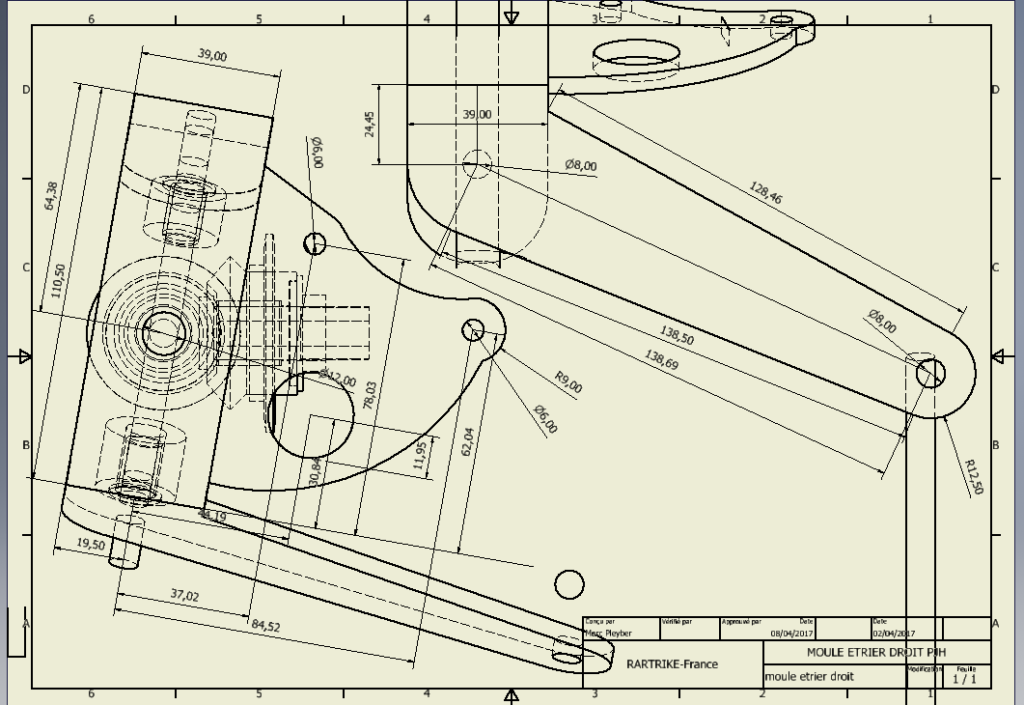
EMPREINTE MOULE ETRIER DROIT